Kevin Kelly is the Managing Director of Kilmarnock (Scotland) based cable manufacturer Altas Cables. Here we visit their headquarters, take a tour, have a demonstration of their cable range and talk to Kevin about the history of the company, the company’s design philosophy, a teensy bit of football and we avoid studiously the subject of Brexit.
HP: When did Atlas launch and how did the launch come about?
KK: Atlas cables was originally conceived around the year 2000 as an own-brand cable product for the UK specialist retailer buying group Mountain Snow. As Atlas expanded its reach in the UK and internationally the brand was purchased by a group of investors who helped provide the infrastructure and support that was needed to fuel the business growth into export markets. Atlas became more than just an in-house solution for Mountain snow but a brand in its own right supplying many more UK retailers and finding distribution around the world.
HP: Were you involved from the get-go and if not, who were the main players?
KK: I arrived relatively late to the party and purely by accident (2010). I had set up a small CI business but also kept my hand in with some electronic consultancy design work and during my research of local companies I came across Atlas. I had been in the Hi-Fi and AV business for 25 years and although Atlas was in my home town I had never heard of them. I called up Atlas and spoke to John Carrick who was a bit rude on the phone – I new immediately that this was something worth investigating!
John retired around four/five years ago and this left Jon Turner as the last of the original investors but certainly the most committed.
HP: You worked for various High Tech companies, in what capacity, for how long and how has this influenced how you go about business?
KK: I have been blessed to work with class-leading companies all my life; Pilkington Defence systems, Linn, Phillips semiconductors, Loewe and Atlas.
During my career I have occupied the following positions: Electronics design engineer, Strategic design-in- Engineer, Sourcing manager, Head of Sales and Marketing and Managing Director. If you ask me what I enjoy most it’s the engineering, it’s the most challenging but most rewarding …. When you get it right!
I was lucky to be involved in Linn’s original Digital Audio research that led to great products such as the Numerik studio mastering system, their first CD players the Karik and the Mimik as well as many other great products.
I have a strong team-based work ethic, single status, no one treated any different, all working in different roles but all pulling together in one direction.
HP: Atlas is based in Kimarnock, Scotland, how important is this area to you and the company and would you ever consider moving out of the region?
KK: Kilmarnock was a proud industrial town; Massey Ferguson (tractors), Glazier Metals (bearings), BMK (carpets), Lace manufacturing and the home of the world-famous Johnnie Walker whisky. After 190 years in our town its heart was torn out by the closure of the Johnnie Walker factory, Johnnie Walker must have been turning in his grave. I am committed (despite the difficulties) to manufacturing Atlas products in Kilmarnock and to create opportunities for local people to have sustainable high-quality jobs available to them.
HP: Atlas recently bought the facility we visited, how important is this to the growth and future of the business?
KK: Part of our commitment to the staff and the town was our decision three years ago to invest in a bigger manufacturing facility within cycling distance of my house! We tripled our footprint and built new demo rooms etc allowing us to grow significantly last year. We are a company that plan all our activities and our strategy for steady growth is bearing fruit with increased product quality, improved efficiency and better design processes.
HP: What would you say is the philosophy that underlies Atlas cables?
KK: We are an engineering and material science company that love music, we believe that whenever there is a sound quality difference between two products, we (Atlas) should be able to explain why that could be. We believe that all cables can be differentiated by the five following attributes;
Conductor Quality
Dielectric efficiency
Plug Quality
Manufacturing process
Screening efficiency
HP: You mentioned that you don’t use solder at all in your cables which is very unusual, what do you see as being the benefits of this process and how does it work?
KK: We don’t believe soldering is necessarily bad, however when we originally chose our preferred conductor material to be OCC copper this necessitated the use of cold welding. The reason being that OCC as a material doesn’t really like much “post-processing” especially variable high temperatures (soldering or extrusion). As we didn’t want to solder the conductor material this meant we had to design and manufacture all our own plugs. So, over the years this has developed into our brand-defining manufacturing processes. We don’t solder or silver plate any of our analogue cables and by not soldering we deliver very consistent products and have virtually no variability product to product.
HP: You’ve written a white paper on “velocity of propagation” which talks about the importance of the dielectric used. Can you explain to Hifi Pig readers the findings of the paper, what this means to the perceived sound of a cable and how you implemented your findings on your “High V” cables?
KK: We try as far as possible to be transparent and publish our cable specifications. We are often asked about how we go about designing cables and its pretty systematic. Generally, the wider the bandwidth of the cable the more natural and accurate the sound, therefore one measurement technique that gets you started is to measure/design to a Velocity of propagation figure. This is a ratio of the speed of light to the speed of an impulse travelling through any material (dielectric). This gives you a base performance level and then you can start looking at geometry, cable plug termination and delivered sound quality.
HP: The plugs and connectors Atlas use differ from product to product, explain the differences and the effects you feel the differences have on the performance of a cable.
KK: The clear benefit for us is the lack of solder in the junction between the conductor and the plug body. When you lose the non-essential material (solder) you improve the chances of maintaining signal integrity. We also change material in the plugs to match as best as possible the dielectric material in the cable. For example, we have one design for XLR plugs, however, we have two sets of different pins on the plugs, OFC pins with Polyethylene dielectric for OFC cables and OCC pins with PTFE dielectric for OCC cables, same for our RCA cables.
HP: How do you carry out your R and D and who has the final say with a new product?
KK: We try to design in performance with simple clear engineering methodology, then measurements and lastly plenty of testing. We have a listening panel and again the team needs to decide.
HP: Do you find that most users of Atlas cables dip their toe in the water with the lower end cables and then move up through the range? I suppose what I’m asking is “Once a customer buys into the Atlas brand do they stay loyal to the brand?”
KK: We were lucky to win the What Hi-Fi award 2011, 12 and 13 for our entry-level analogue interconnect the Element Integra, which is remarkable for a small company such as us as we do compete with some big powerful companies. We talk to customers every day and many of those original Element customers have progressed through our range to Mavros and Asimi, its quite a journey.
HP: You recently launched the unashamedly high-end cable in the form of Asimi, how does this cable differ from its predecessor, what are the sonic benefits and is it aimed at a specific marketplace?
KK: Asimi OCC silver loudspeaker cables have been with us for many years however when the time came to rejuvenate the product line, we as you can imagine were a bit anxious. As always we decided to commit 100% however, we also took the unique step for us of working with a designer to improve the delivered quality” of the product. Whilst we worked on the Conductor design, improving the dielectric efficiency, implanting new RF screening techniques and developing the manufacturing process others worked on the customer experience. The result is the most advanced cable we have ever made, it’s accurate, open natural and …. Beautiful.
It’s unashamedly expensive as we used the best materials around but we also delivered a Bespoke design that can fit into the world best HiFi systems.
HP: We heard the benefits of Grun quite clearly, explain to readers what Grun is and what it brings to the table sonically.
KK: We could talk for days about Grun, suffice to say that it came about from years of continuous improvement to our products and manufacturing processes. The original idea launched with the Asimi Ultra RCA three/four years ago and that was to improve the RF performance of cables by eliminating inter-screen distortion introduced by the manufacturing process. We developed the “dual drain” technique to eliminate this issue and that provide a future pathway to providing the external Grun connection – this is the ability to connect the very important screen to an external grounding source thereby providing a direct pathway to eliminate all Rf distortion in the signal path.
HP: Let’s talk digital cables. The naysayers will say that USB etc is a standard, believe me, we have the discussion almost on a daily basis, and so there is no way cables with different make-up can make any difference, but our experience, both at Atlas and elsewhere, is that more often than not digital cables have the most profound effect, how would you go about explaining the effects of digital cables?
KK: Having spent years and years at a bench with a spectrum analyser I can tell you that the interconnections between product be that analogue or digital make a huge difference to the delivered audio quality in a system. As previously stated my initial profession was as a digital electronics engineer so I’m into “bits”12. In all systems the ability extract information from the data is critical, if you make the extraction of digital data easier for any receiver then there exists the potential for higher fidelity replay (audio and video) upstream. Back in 1987, I developed a technique called the sync link that was used on early Linn CD players and DAC’s. The Sync link when connected steered the DAC to become the master and the CD player became the slave. This reduced time-based jitter at the critical digital to analogue converters and resulted in better sound. Today advanced screening techniques e.g. Grun also help to reduce the RF system load and therefore again improve performance.
HP: Moving away from cables, you play in a brass band, what do you play, how often and what accolades has your band won?
KK: I started playing when I was 11 and now 47 years later, I love it even more. I play at rehearsals at least twice per week and of course I still do home practice. Playing music with your buddies is a privilege and every night I give thanks to my old dad who picked up on a comment and organised my first lesson. We are also a competitive bunch and regularly contest all over Scotland and occasionally play around the UK. We have had our share of success as Scottish champions in various grades but the enjoyment is playing well and heading to the pub having played some great music together.
HP: Do you think playing an instrument has helped you in putting cables together and what do you listen for in a cable?
KK: I certainly know the difference between noise and music, the later only happens when you pay attention to detail, when you allow the music to flow, when the cables and interconnection between products are transparent. Accuracy, openness and natural sounds are easier on the brain and stimulate the brain to enjoy and this is what we strive to do.
HP: At time of writing Kilmarnock FC are fourth in the SPFL, where are they going to be at the end of the season?
KK: Well at last onto important stuff …… I don’t really care as I’m a supporter however if we get to third then Steve Clarke should be knighted!!!
HP: Finally, this interview will be published very shortly after the deadline for Brexit. What impact has the uncertainty around Brexit had on the business in terms of planning etc?
KK: Let’s not talk about it!!!!
HIFI PIG VISITS ATLAS FACTORY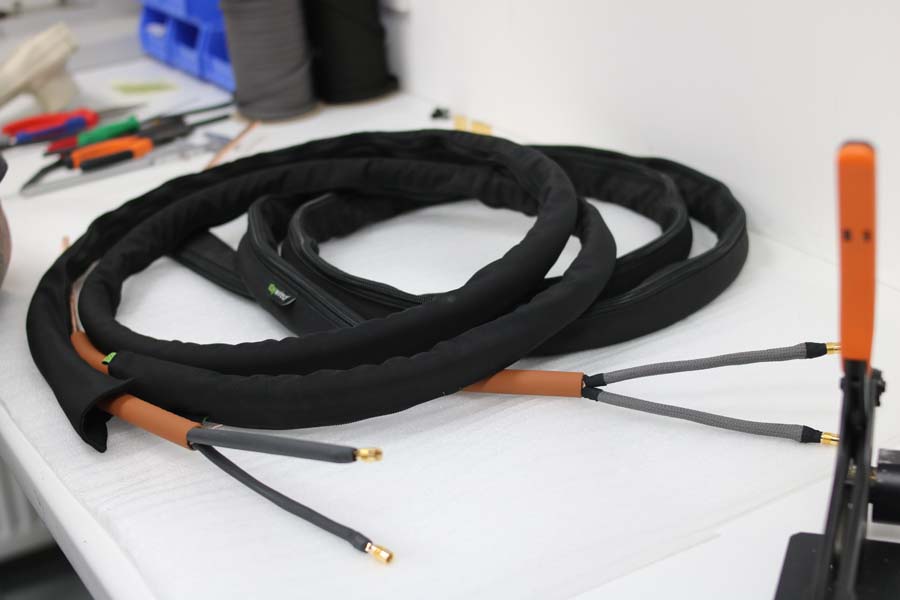
Hifi Pig visited the Scottish headquarters of Atlas to gain an insight into the way they do things way up in the North. The weather was freezing but the welcome was warm and we thank Kevin and the team for taking the time out to spend with us.
What struck me first is that the production process is meticulous with higher-end products being made to order and with everything signed off along the production of each item.
After a tour of the factory (see pictures) we went into the distribution area of the building and it is surprising to see just how big an operation Atlas really is, with racks and racks of product and this is encouraging to see. I was also encouraged to hear that the vast majority of design and manufacture of everything is done in Scotland wherever possible, with Kevin mentioning that having such control over manufacturing gave Atlas a consistency in the finished product and that all the products, having been designed by Atlas, were unique to Atlas.
One of the interesting things that Kevin was keen to talk about was not just the cable (wire) geometry used in their cables but also the dielectric and the actual plugs which Atlas see as being as big a part of the overall performance as anything else. Atlas doesn’t use solder in their plugs and instead choose to use a technique known as a cold-weld which is essentially done by a special crimping tool.
We were also treated to a demonstration of the company’s products by Martin McCue (pictured below) and Kevin, starting off with the company’s entry-level model, the Integra, of which there are three different models, and working through to the top of the range Mavros and Asimi cables.
The differences moving up the range are clear and whilst some people still eschew the idea of cables sounding different, I really do urge them to go take a demonstration such as this. One of the biggest surprises on the day was the improvements with the addition of better digital cables. You know, right, digital cables all have to sound the same because it’s a standard that either works or not and it’s zeros and ones? Not so on my experience and once again on a cable demonstration it was the digital cables that we perceived as having the biggest overall effect.
One of the more interesting things that Atlas have recently introduced is their Grun adapters that are available for Mavros Ultra and Asimi Ultra interconnects and Mavros speaker cables. Grun essentially, and I’m quoting their website on this on this: “One of the biggest obstacles to achieving the performance levels our equipment is capable of is noise. Low levels of RFI (radio frequency) and EMI (electro-magnetic interference) and noise on the signal ground all subtly modulate and degrade the overall noise levels of the system.”
“Ironically, this is generally only noticeable when eliminated – even though much of this ‘noise’ is theoretically at frequencies beyond the range of our hearing. The main sources are noise in the mains supply and component ground connections – mobile phones, ‘wallwart’ chargers and wifi networks are major offenders – while a percentage is actually generated within the equipment itself. Generally, things have got worse with the advent of computer audio.”
“The Grun Coherent Earthing System addresses these issues by providing ‘independent’ earth for users of Mavros and Asimi Ultra interconnects and Mavros speaker cables* with the new Grun configuration.”
Do I understand all that, well no I don’t but the effects on what comes out of the speakers are clear and their point about “… generally only noticeable when eliminated” is absolutely true in this case.
Again thanks to Kevin and the team for the wonderful hospitality and we hope to see you all again really soon.
You must be logged in to leave a reply.