HiFi PiG’S OSCAR PAYS A VISIT TO AUDIO NOTE UK
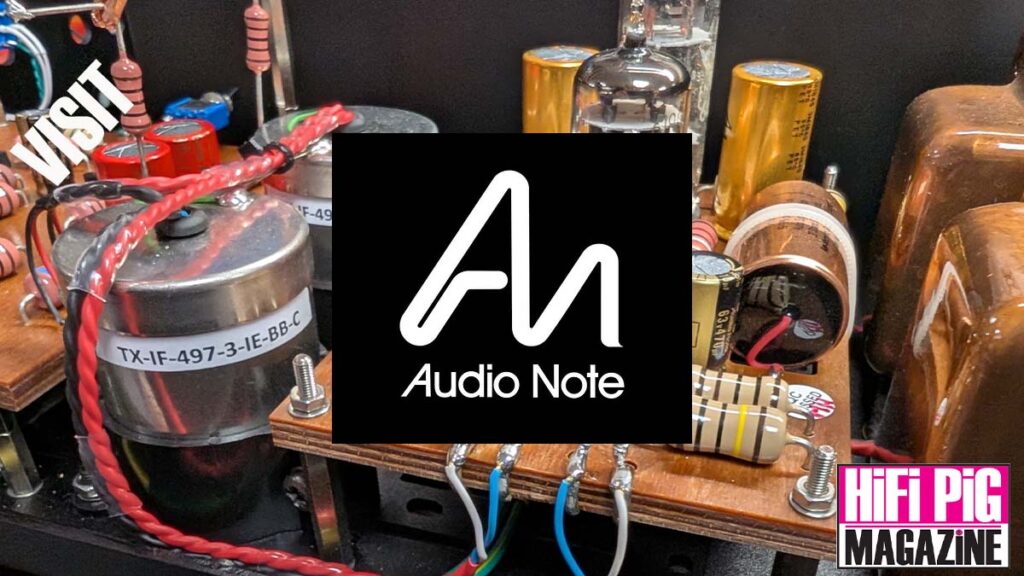
ALL IMAGES AND TEXT ARE COPYRIGHT HiFi PiG AND MAY NOT BE USED WITHOUT PRIOR WRITTEN CONSENT FROM THE EDITOR
On a cold February morning, Kelly and I set off on a short drive to visit Audio Note UK, which is a mere 30 minutes away from where we live. Located on a small industrial estate in Partridge Green, Audio Note UK manufactures a wide range of electronics and speakers. This UK site is their main base and they make all their amplifiers here, along with the field coils for their speakers, whilst their CD players and speakers are manufactured in Europe (with some of the parts coming from the UK factory). I was warmly greeted by Micky, who is a familiar face at UK shows, and quickly introduced to Peter Qvortrup and his son Daniel who showed us around the factory.
Before seeing how the kit is made, Peter gave me a little bit of his background story, from working for Maersk and driving vans of vintage kit from the UK back to Denmark (where he is from) to restore and sell on; to receiving his first bit of silver cable in the late 70’s, something that was a revelation to audiophiles back then. He detailed that in one of his shipments from Japan, of silver cable, there was an MC cartridge from his supplier which was the IO2. Initially lacking a suitable transformer, he sourced one from Japan and then put it up against the current competition, at which point according to Peter, the IO2 made the competition sound broken. It’s this passion for high quality audio that led him to pursue a lifetime in audio, which started when he moved to the UK in 1983. Shortly after moving to the UK, he got called to assist a friend with an audio shop just off Sunset Boulevard in LA (USA). Helping run the store he was also lucky enough to spend quite a lot of time at the audio bars in the area which hold a rich music history. After only 7 months in the US, Peter came back to the UK and purchased a HiFi store in Basingstoke. The rest, is as they say, history – and Audio Note UK released their first product in 1991.
A few things stand out from this conversation with Peter, firstly he has led an incredibly interesting life and secondly, he really is very proud of the quality of Audio Note UK products. He mentions that it is not the overall power that is important, it is rather the quality of said power that matters. When asked about measurements, and the fact that on paper valves are “not the best” – he mentions that the current way of measuring audio equipment cannot quite capture everything and that we only measure certain parameters which do not tell the full story. I did ask if there was a reason they only make valve amplifiers, to which he replied that they only make equipment with whatever works best, no matter the topology. Another interesting quote was that, if you copy an old design (for example field coil speakers), then you must first understand why they were made in the first place, at which point he mentioned that he spent a lot of time with some of the original designers of revered audio equipment such as Klipsch and Marantz. Trying to understand their designs and what made them special, is the key to understanding why certain technologies were used and their applications in audio.
We touched on world politics, philosophy and the rise of AI, and could have spent all day chatting, however, it was time to move on to seeing how Audio Note UK make their amplifiers and other kit. First off, they have a warehouse with a few stock products such as their CD players, and a test area for soak testing new amplifiers that have been built. After they are soak tested, they get tested again and the valves are then matched within the amp before being sent off to the customer.
The next stop was the service department, I’ve always been a fan of service departments and the number of bits and bobs they always have lying around, as well as seeing what goes on in repairing the kit. They had a few bits being tested and repaired, as well as an exciting new product that is being worked on and we hope to be able to share more details on that in the future. Whilst in the service department Daniel showed us that they use different materials for different circuit boards within their products, and the higher up you go the more they tend to use their special wooden boards which are specially made from specifically layered sheets of wood. A circuit board resonates, like any other material, and this can affect the sound quality. They have some standard printed PCB’s, then a higher quality board with thicker traces, then their wood ones with point-to-point soldering right up to their Legend amps which use wood boards with integrated channels so the wires on the underside of the board sit flush. It’s also the case that they have three different lines of electrolytic capacitors which all have a different sound, you cannot just cram a product full of Kaisei capacitors and expect it to sound the best, there is a balance when tuning the product, to fit the right capacitors in the right places to ensure the best sound overall.
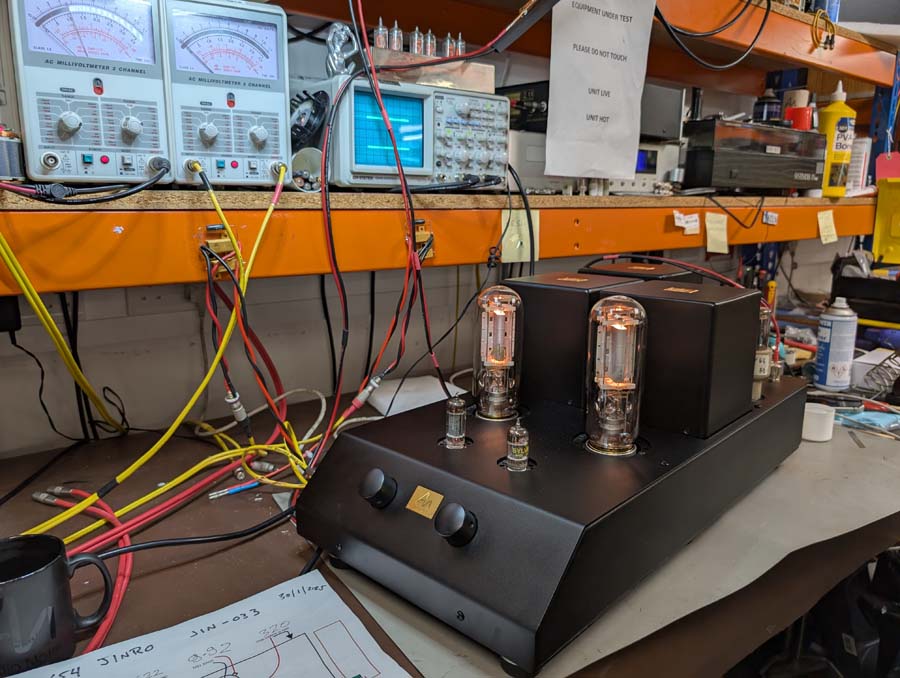
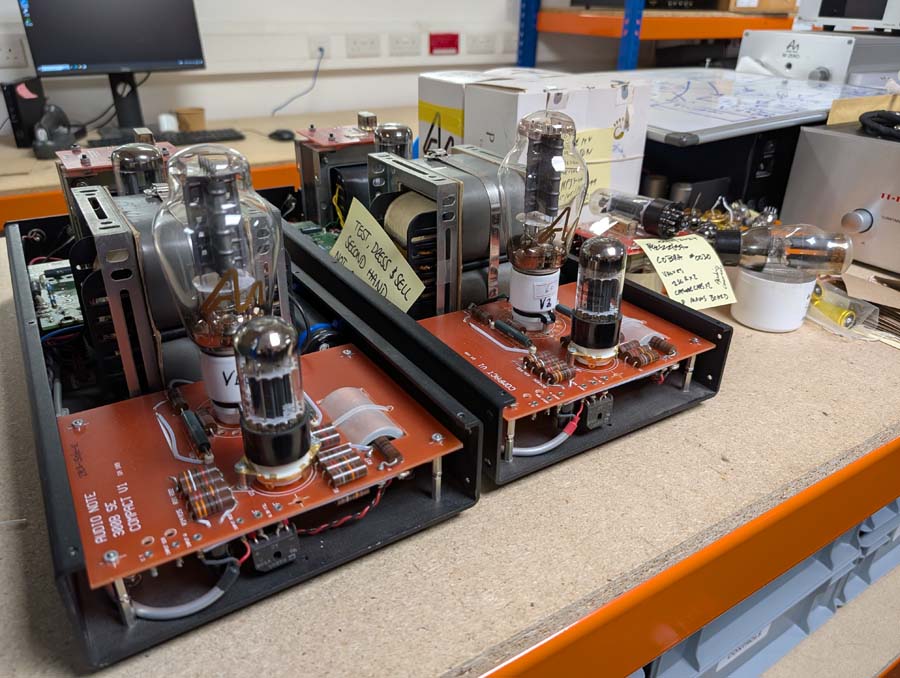
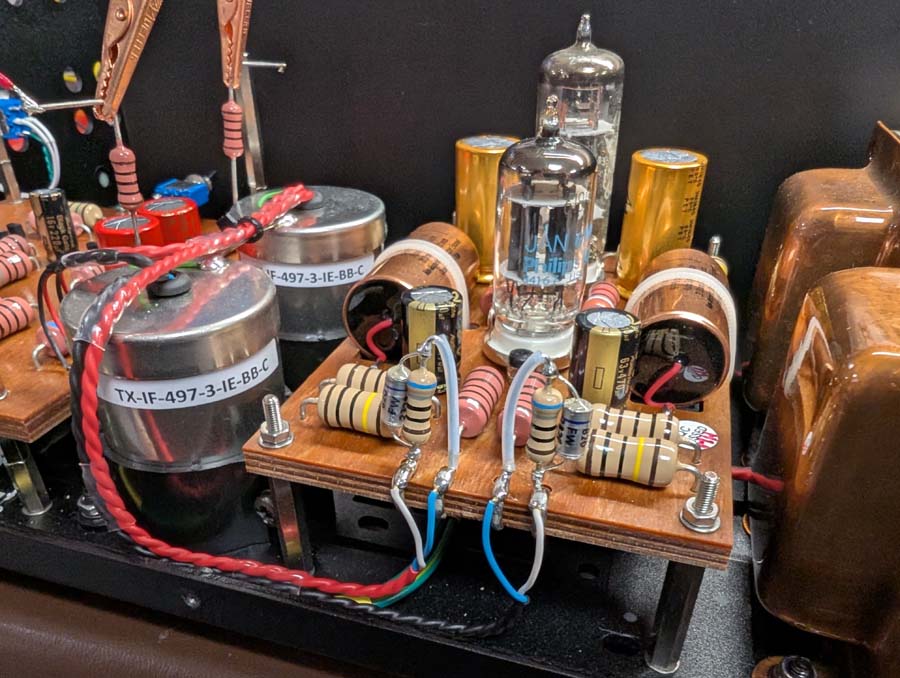
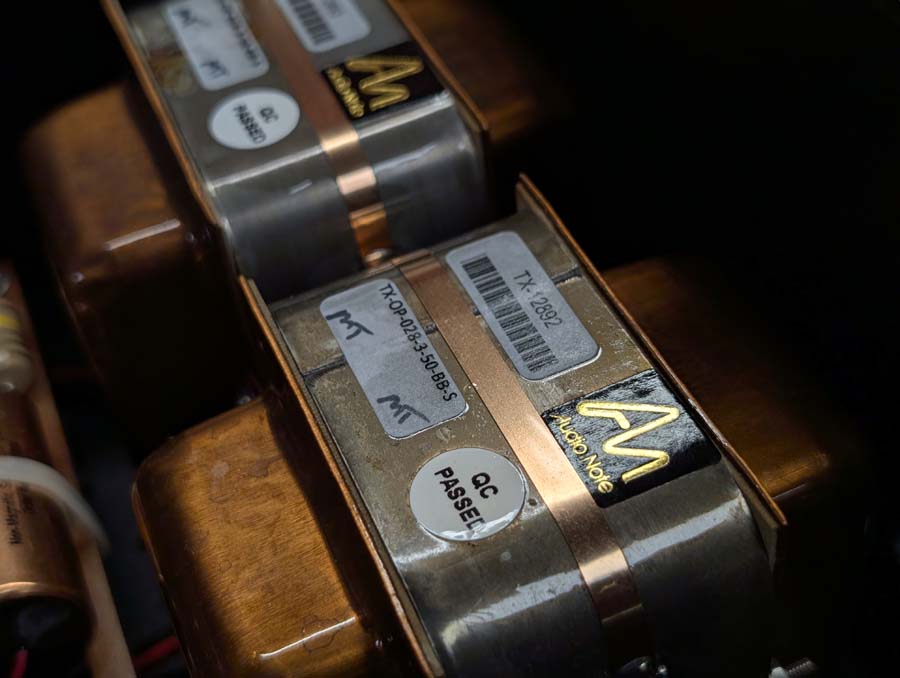
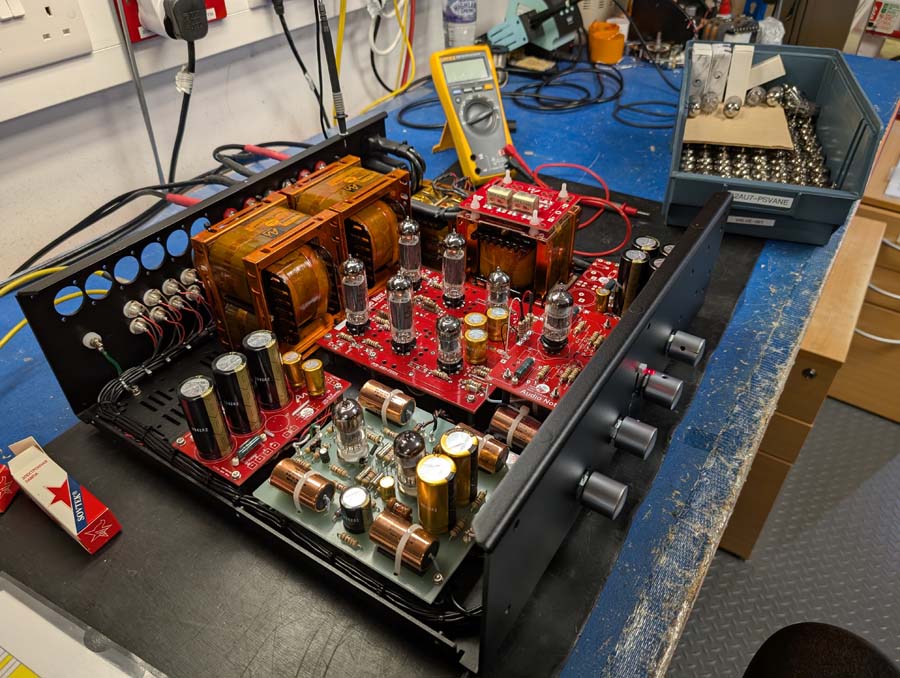
On from service, we got to see the main production line, with a few different sections for different products. We got to see one of their stepped potentiometers which go into the higher-end products, and also where they hand make their cables (the cables are made to their specification and then terminated by hand in the UK).
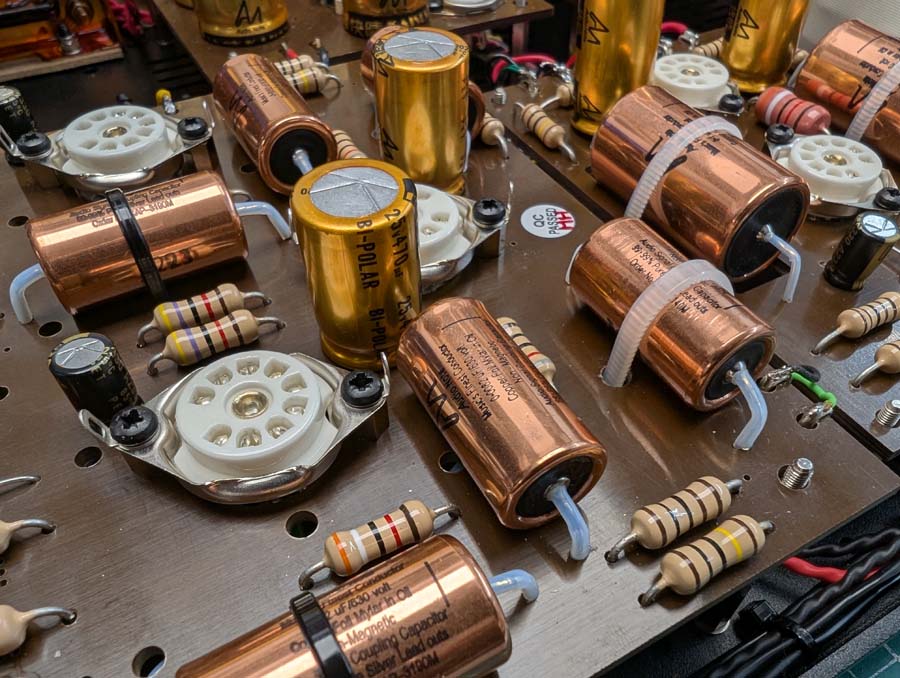
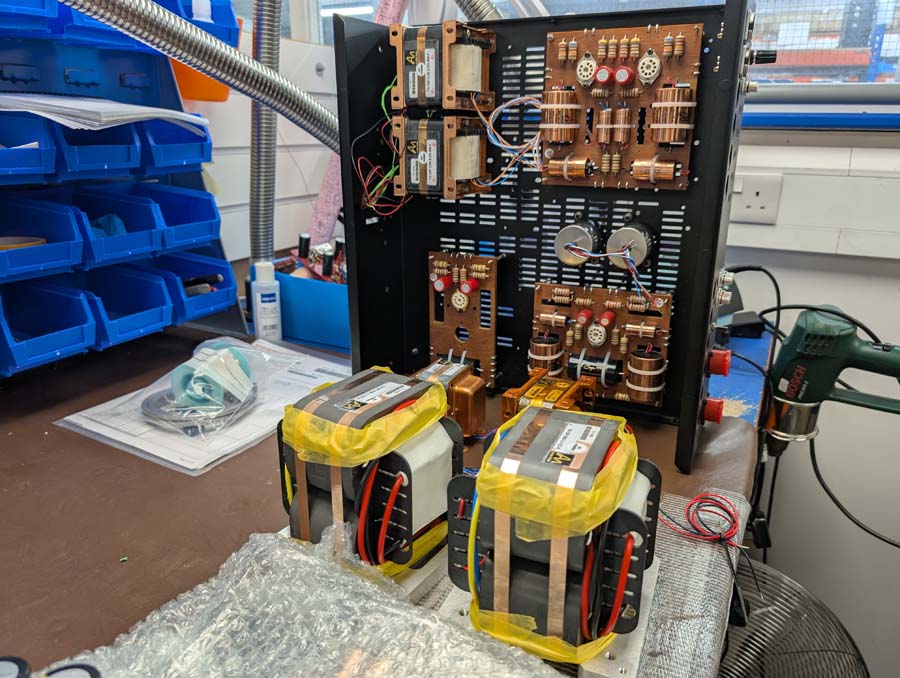
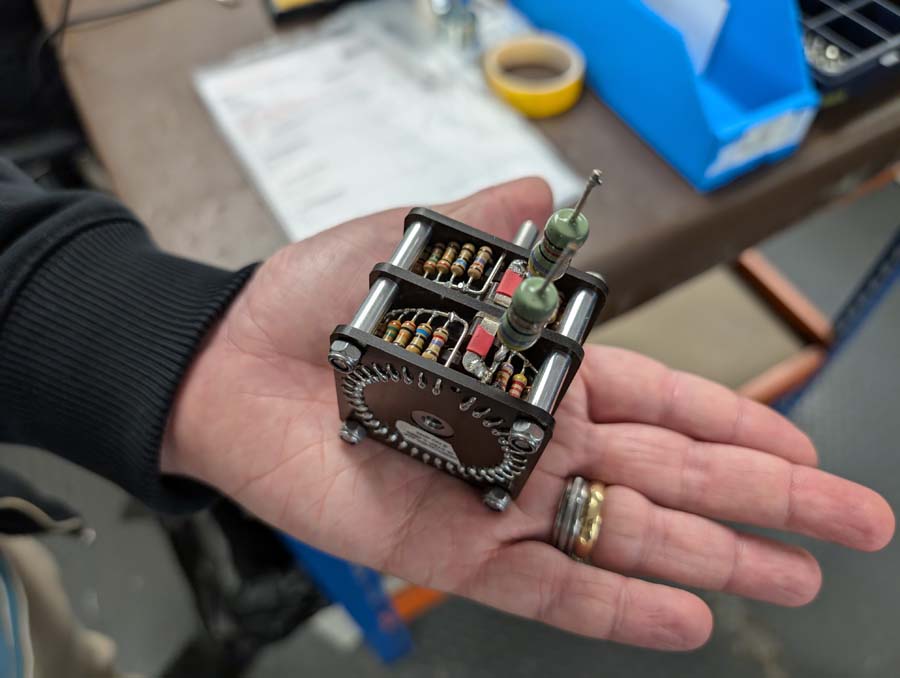
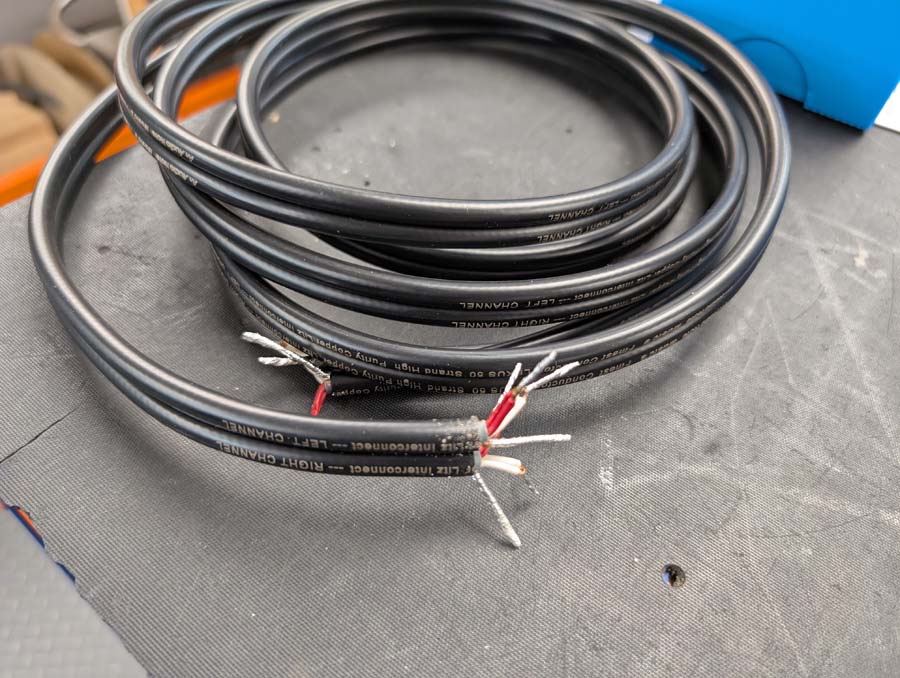
Upstairs is their stock room, unlike most manufacturers who hold just enough stock for their production runs, Audio Note UK keep a vast amount of stock to be able to deal with any shortages should they arise. This allows them to continue manufacturing without delay, as we all know during COVID a lot of companies struggled to get components. It was mentioned that they hold around 4.5k stock lines, this includes some Black Gate capacitors which Peter bought huge stocks of when they announced they would be discontinued (allowing them to still use them in certain products). The stock room is quite something, capacitors, connectors, circuit boards, cables, resistors and more. Speaking of resistors, Audio Note UK use Niobium resistors, a material that is related to Tantalum. As far as I know, they are the only company using this material in audio resistors and, it was a material discovered by Daniel whilst teaching English in Brazil – to miners who were mining it. The machine that makes the resistors is also only running to make these specific resistors, had Audio Note UK not made these the machine would have been decommissioned and dismantled to make way for something else. Valve sockets are also something that quite often cannot be sourced to satisfactory standards as a whole piece, so they keep ceramic bases, pins, springs, and clamps to be able to make up their own sockets to use in their amplifiers – these ensure a tight grip on the valve’s pins for a lifetime of use.
On to the final assembly line now and here you got to see an array of finished parts being assembled into their chassis ready for testing. They had a pair of The Legend amplifiers half built and wow, are they heavy. They are made in pairs and to the specification of the customer (in terms of valves they want to use), each pair is named after a famous pianist instead of featuring serial numbers.
Now for the transformer section, which includes manufacturing the coils for their field coil speakers too, there were also CNC machines for the boards and 3D printers for prototyping too. We got to see step-up transformers for use with MC cartridges being made, and the wires being set up for some field coils to be wound. You might notice that the transformers are covered in orange resin, this is done at another unit down the road, using a vacuum impregnation process that helps seal the transformers. Audio Note UK has one of only two of these vacuum impregnation machines in the UK (the other belongs to the distributors of the machine). Another step to ensure they have absolute control over the manufacturing of their transformers and overall quality of the product.
Next to this was the capacitor making room, where they make their copper and silver foil capacitors. The machines being used are old yet beautiful, the company bought them off the man who used to wind them for the company once he retired, they also purchased the stamping machine for the labels. There is a big vibrating machine that polishes the capacitors (using ceramic beads) once they have been wound and sealed, they then get cleaned again before being put into stock. It really is amazing seeing a company go to these lengths to make a large portion of their components or have them made to their own specification, it ensures a lot of control over the final product and not having to rely on external parts.
One last trip upstairs allowed us to see the huge stocks of valves that Peter has invested in heavily over the years, some of them are so rare that those he has are potentially the last ones available in the world. I was in awe at the number of valves in this area, thousands of them, all different shapes and sizes, it makes my meagre collection of 6SN7, 6080 and 6AS7G’s look tiny. It also ensures that customers will be able to purchase replacement valves for their amplifiers, for years to come, something that may comfort those looking to invest in an Audio Note UK amplifier in the future. Many of their designs have not changed over the years, which allows them to service most products they have ever made, with relative ease.
We hopped in Daniel’s car and drove 2 minutes to another building that Audio Note UK owns and that houses Peter’s gorgeous collection of vintage Mercedes cars alongside the vacuum impregnation machine for the transformers and upstairs is a listening room/overflow of Peter’s personal vinyl collection.
It was an absolute pleasure to see where Audio Note UK manufacture a lot of their parts and products, along with getting to see the huge collection of valves they have too. Unfortunately, I didn’t get to have a proper listening session as there were building works going on however, I have been invited back once they have finished so stay tuned for another article on that. A huge thank you to Micky, Peter, Daniel and the rest of the Audio Note UK staff for being so accommodating and spending the time to show us around their factory.
ALL IMAGES AND TEXT ARE COPYRIGHT HiFi PiG AND MAY NOT BE USED WITHOUT PRIOR WRITTEN CONSENT FROM THE EDITOR
Oscar Stewart