OMEX SYMPHONY 2A/3A ISOLATION DEVICES REVIEW
Your system sounds a mess and you might not know it. No, really. A new range of isolation devices that can be pretty much universally used for electronics, source components, and loudspeakers, seeks to bring matters into focus – Eric van Spelde takes a listen.
WHAT ARE THEY?
Omex Symphony is a range of isolation devices comprising of two performance levels. Symphony A and Symphony S have been designed as an upgrade to the existing supports on audio electronics and under floorstanding speakers or speaker stands. Each level has two tiers of performance, a twin-layer variant alongside its more advanced three-layer counterpart. Each Symphony device begins with an outer micro-grooved upper and lower disc whose job is to grip the underside of electronics and the surface of a rack shelf more effectively than that of a smooth surface. Omex says this gripping effect has a greater ability to contact and transfer resonances from the equipment and begin the process of eliminating them from the delicate circuitry in one direction and the equipment supports in the other.
The centre piece of each upper disc is what Omex refers to as a tuning fork. This design encompasses a varying metallic density to the disc structure to dampen and control the flow of resonances. Symphony A is machined from an Aluminium Polymer Compound (APC) while Symphony S’ tuning fork is machined from a high-grade brass, which is 24ct gold plated to give a softer barrier between that of the brass and its stainless steel disc. Each tuning fork sits within its own chamber, surrounded by a damping compound, and runs down through the centre of each device.
When it comes to supporting electronics, the tuning forks are designed to never be in contact with the equipment directly, in order not to activate them with the first-hand generated resonances, leaving them to perform their role of damping the upper disc. For loudspeakers, however, the isolators double as a spike shoe, for which purpose the tuning forks feature an indentation in the middle. The design offers a new coupling point through the tuning fork and decouples the speaker or stand from the floor and gives it a ’best of two worlds´ approach, according to the manufacturer
Between each disc of the Symphony layers is an arrangement of three evenly spaced ball bearings. The Symphony A as featured here, uses a stainless steel option (which can be upgraded to ceramic) and Symphony S utilises a fine ceramic option. Their positioning has been designed to allow for resonances to be driven into their pathway, where they can convert and dissipate this energy as small amounts of heat. The bearings have CNC cups machined into each layer for them to comfortably sit within and remain unfixed. The three-layer version has further technical resonance control abilities. This additional centre disc can be referred to as the “scrub layer”. Its primary role is to remain completely decoupled from the top and bottom discs and can be concentrically swung laterally from the vertical arrangement, with its only points of contact being the bearings in between each layer, which are staggered in this arrangement. Each of the devices will accommodate a weight of 45 kg, so heavy loudspeakers won´t be a problem; the cool thing, however, is that within this limit, they are designed to work equally well independently of the weight of the piece of equipment resting on them.
SO, DO THEY WORK?
Oh, yes indeed. I have yet to find a HiFi item on which the Omex isolation devices don´t have a beneficial effect. The first batch of 2A and 3A isolation devices I got, had the layers tied together – which subsequently was changed. I tried the three-layer ones under my Avantgarde Duo XD (modified and run actively with two pairs of SET monoblock amps driving mids and highs) and was instantly rewarded with a much more focused and stable soundstage and significantly improved microdynamics. As a result, vocals were a bit more intelligible, and instruments emerged more clearly from a cleaner background with a more clearly defined space around and in between them. The twin-layer ones under a pair of AudioSolutions Figaro S2 floorstanding speakers, yielded similar results.
Valve amplifiers are particularly susceptible to the ravages of mechanical and electrical resonances, so my next step was to insert a quartet of 2As under each of my Welter 2A3 monoblocks that have been modified (coupling capacitor values reduced to create a high pass filter) to run the high-frequency units on my Avantgarde horns. These were especially critical, as space considerations prescribe the amplifiers standing on their separate power supply units! Unsurprisingly, a distinct improvement along the same lines as with the speakers, was noted.
Meanwhile, further testing on some additions to the range by the manufacturer indicated there were performance gains to be had by changing the way the isolation devices fit together. However, this has the ramification of the layers now sitting loose on top of each other – which doesn´t impact the installation procedure so much when putting them under, say, a preamplifier or a CD-player where you can hold the layers together in the palm of your hand (or just hold them in a pincer movement), but when I wanted to put the ´new´ three-layer versions under the AudioSolutions speakers (34 kg apiece) it quickly ended in a mess of ball bearings rolling on the floor as the slightest movement had the speakers´ spikes knocking the top layer off the lower ones… I quickly reverted to the original version in twin-layer guise, which netted the significant improvements mentioned above. I didn´t try to exchange the ones under my 91 kg Avantgardes, either… The trick, in these cases, was to pop a piece of low tack tape like masking or electrical tape across the disc joints, position the isolators and then remove. The manufacturer has a neater solution to this now with the addition of included black circular removable and reusable placement stickers that leave no residue on the isolators, simply place one on two opposing sides, place the isolator where you need it and then simply remove them for use again.

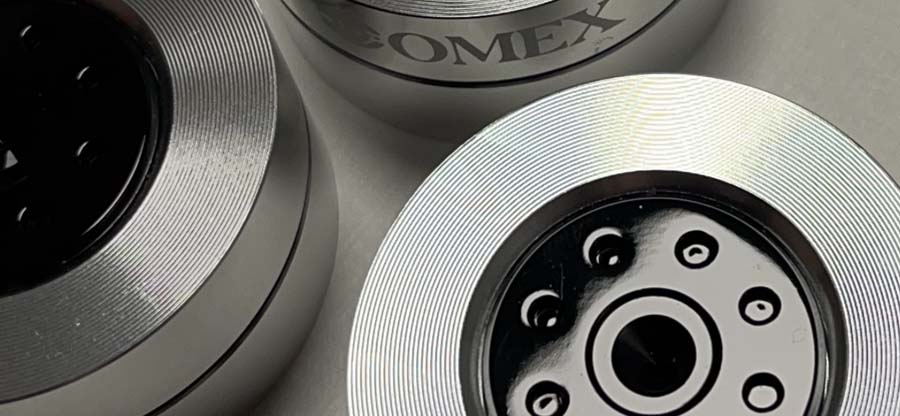

Do I detect any differences between the ´old´ versions where the layers are locked together, and the new ones? I´m not sure. Frankly, I was delighted with the improvements when placed under various pieces of equipment as it was – coming from a rather suboptimal situation with equipment standing on floors, small Ikea Lack tables (not as bad as it sounds – their lightweight, but fundamentally stable construction does have benefits in terms of slow energy storage) and anywhere that the cramped domestic conditions, as well as cable lengths, would allow – and my first instinct was to leave well enough alone. In most quick equipment swapping and reshuffling scenarios for review purposes, the difference between the two versions seemed to pale into insignificance compared to the strong effects of having the footers in the first place. However, the newer configuration does open a window of opportunity for subsequent tinkering, replacing the ball bearings with the ceramic versions of the higher end S range, or titanium ones that will be available in the future. In a long-term optimisation scenario, this could well be of benefit, helping to eke a final couple of percent performance out of an otherwise well-established and optimised system – which is something I intend to do on my personal ´core´ system.
Pre-amplifiers, phono stages and their power supply units all benefit from having the Omex isolators as an interface between them and the surface they´re sitting on, in much the same way as with the speakers and the valve amps, albeit to a lesser extent. The cumulative effect, however, of the sound becoming more stable, precise, more relaxed, and more dynamic at the same time with a lower noise floor uncovering a lot of inner detail that had gone under before, however, is noticeable with every additional component you put on the isolation devices – even ones you might dismiss as ´uncritical´ or ´insignificant´ beforehand. With a HiFi consisting of as many boxes as my main system, this might grow into an expensive habit – albeit a satisfying one.
Rather surprising, however, was the effect of the Omex isolation devices on a Michell Gyro SE turntable that itself features a well-developed isolation system in the shape of a subchassis which is suspended from three spring/damper ´towers´ that stand on conical feet. Not unlike the very expensive Levar Magnetic Absorbers under my mass-loaded Acoustic Signature turntable which is similar in price to the Gyro, the isolators still took the overall performance to an entirely higher level, adding the sort of stability, focus, and detail retrieval that one recognizes from ´statement´ turntables with price tags deep into five figures (and, more often than not, a footprint to match).
AT A GLANCE
Build Quality and Features:
Exquisitely machined and engineered and attractively presented, these do have the air of a luxury product. As a result, the pride of ownership factor is at the very least commensurate with the price tags. The isolation devices are et the same time relatively small and unobtrusive, and especially the twin layer versions don´t add a lot of height to the equipment when sitting on a rack shelf.
Sound Quality:
Under every piece of equipment and on any surface we tried, the isolation devices allowed for more stable, more focused, more organised, more palpable soundstage, with significantly improved microdynamics, lifting subtle details out of the normal background of grain and fuzz.
Value For Money
Yes, they´re a bit expensive. No, we wouldn´t necessarily put them under a £199 amplifier or CD-player (although they would probably lift their performance beyond their price bracket). Under loudspeakers, however, they give at least the same level of improvement overall than still more elaborate and expensive solutions, while their cost-performance ratio under turntables and valve amps also strikes me as outstanding. And if your other electronics are even remotely ambitious and costly, frankly you owe it to yourself to see what they really can do…
We Loved:
The overall level of improvement the devices yielded with any sort of equipment; their universal application making it fun to swap them around under various items we had around for review or otherwise, the versatility and the possibility to ´tune´ them further with different ball bearing materials, the way the tuning forks are shaped making them an excellent match for spikes or cone-shaped footers; we also found that they improved the look and neatness factor in many applications.
We Didn´t Love So Much:
Ball bearings rolling on the floor, but then I had only myself to blame for it… Seriously, however, doing a complete system runs deep into four figures depending on your configuration, even with these ´basic´ ones and you will want to do that sooner or later (oh, and you probably will want to try the more expensive ones at some point, too). The gains prove addictive like that…
Price:
Omex Symphony 2A: £300/set of four
Omex Symphony 3A: £400/set of four
Eric van Spelde
TECHNICAL SPECIFICATIONS
OMEX SYMPHONY A
Symphony 2A – 72g each – 546g set of 4 boxed
Symphony 3A – 105g each – 665g set of 4 boxed
Dimensions: 2 disc – 20mm tall x 40mm diameter. 3 disc – 30mm tall x 40mm diameter.
Omex Symphony A will accommodate a weight of 45kgs each.